Plating on 3D Printed Parts & Components
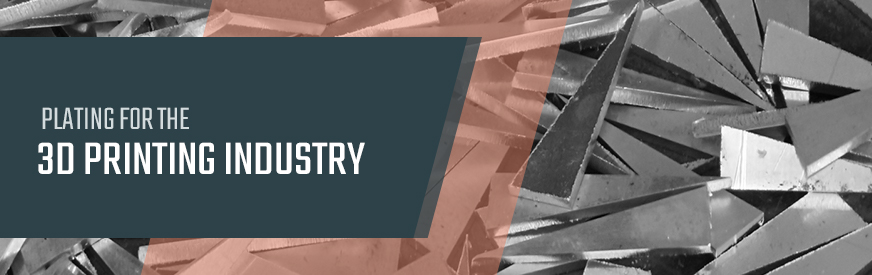
3D printing has quickly gained steam in both commercial and industrial applications as a flexible and efficient means of manufacturing, both on a small and large scale. While versatile, the process is currently limited in the types of materials it can work with, primarily using thermosetting plastics. To add a new layer of functionality and strength to these parts, many manufacturers have turned to plating services.
What Is the 3D Printing Process?
3D printing, alternatively known as additive manufacturing, is a process where an object is built up in an additive process using a 3D digital design. The process essentially uses this 3D design in an STL format, sending it to a 3D printer. This printer effectively "prints" in the same way as a traditional 2D printer, depositing material on top of a substrate. The primary difference is that it deposits layer after layer of this material atop itself to form the final product.
The 3D printing process comes in several variations using different technologies and materials. For example, SLS, or Selective Laser Sintering creates a 3D product by directing lasers into a vat of thermosetting polymer, solidifying the material point by point into the final product. The FDM or Fused Deposition Modeling process, on the other hand, uses an extrusion process to deposit heated material into open space. Each of these processes use different equipment and methods to produce similar results.
What Are 3D Prints Made Of?
The material a 3D printing process uses depends on the technology involved. Thermoplastics, including polycarbonate, polystyrene, polyacetal, polypropylene and blended nylons are most commonly used. Polyamides, epoxy resins, and other types of plastics and polymers are also used. Some 3D printing methods use silver, titanium, steel and wax, though these products are rarely plated. In many cases, manufacturers will seek to plate a plastic product.
The type of material used is an important factor to consider when plating plastics, however. The more chemically resistant plastic, the more difficult it will be to plate because of the process used to plate plastics. The plastic plating process uses a chemical surface treatment as a preparatory measure to improve adhesion — both this chemical and the plating process as a whole are discussed later in this article.
How Is 3D Printing Used?
The versatility of 3D printing and its ability to form complex shapes more easily than other manufacturing methods has made it an indispensable tool for many industries. Just a few examples include:
- The Medical Industry: 3D printing is seeing extensive use in the medical industry, especially when it comes to the production of custom prosthetics and medical equipment. There are even ongoing studies considering the possibilities of organ and bone printing.
- The Design Industry: Engineering and design industries have come to love 3D printing for its ability to build prototypes and models from scratch in a matter of hours. In a single day, a designer can go from a computerized model to a physical one. This has helped designers and engineers in all fields, from the aerospace industry to architecture.
- The Automotive Industry: In addition to their designers' uses of 3D printing, the automotive industry has gotten a lot of use out of the technology. 3D printed cars are now available for viewing, and many custom parts are now 3D printed to save time and resources.
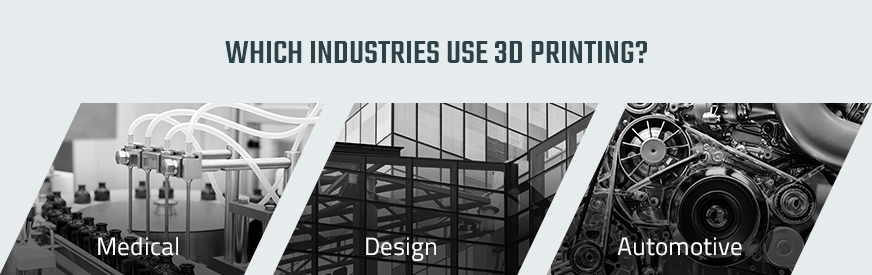
These examples represent only a fraction of what 3D printing is capable of, especially when you factor in the functionalities added through plating.
What Is Plating?
If you've worked with Sharretts Plating before, you're likely familiar with what plating can do. Essentially, plating involves covering a part with metal to lend the part additional benefits and functionalities. The process has been around for over 200 years and is used in several industries as a valuable manufacturing tool.
How Has Plating Been Used on Plastics?
Though more commonly used to plate metallic parts, plating can be used on plastic parts as well. The method has been around since the 1960s after experimentation brought about a chemical surface treatment to improve bonding between a plastic substrate and its metallic coating. Plated plastic became commonplace throughout the automotive industry in the 1970s to reduce the weight of automotive parts and quickly spread to other industries through the 80s.
While demand for plastic plating waned through the 90s and early 21st century, demand for plated plastic products has increased again as lightweight cars have again become a priority and 3D printing with plastic has come into vogue.
What Are the Benefits of 3D Print Plating?
Many 3D printed products are produced with a plastic material rather than a metal or organic material. Often, this results in a product that is lightweight, yet relatively weak to external forces and conditions. That's not to mention the outward appearance of these parts, which can vary greatly in color consistency and aesthetic appeal. To all these problems, plating offers a solution.
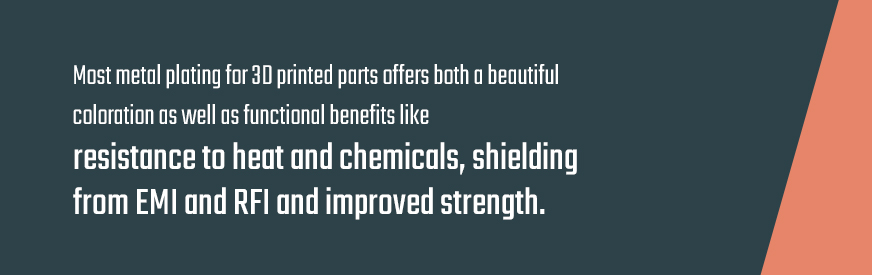
Plating for 3D printed parts offers both aesthetic and functional benefits. A coat of a metal like silver, for example, can increase the product's outward appearance while also improving its resistance to corrosion. In fact, most metal plating for 3D printed parts offers both a beautiful coloration as well as functional benefits like resistance to heat and chemicals, shielding from EMI and RFI and improved strength.
Request a free quote
For 3D Print Plating
How Are 3D Prints Plated?
Plating onto 3D prints is quite similar to the plating process for plastics is most cases, unless the print is made of a metallic or organic material. The exception is that the substrate must be 3D printed before the plating process can begin. Just like with plastic, however, the part needs to meet finishing and temperature requirements before starting the process.
The actual process for industrial plating for 3D printed parts usually starts with an electroless plating process, which "metallizes" the plastic to deposit an initial layer of metal. Once this layer is deposited, another layer can be applied using another method to produce the final finish. The initial electroless plating process for plastics follows this basic structure:
- Cleaning: Before anything else, the surface of the part has to be thoroughly cleaned, usually with a mild alkaline cleaner. This cleaning process removes any oils, dirt and debris from the surface of the part, which can interfere with the plating process and result in low-quality adhesion between layers.
- Pre-Dipping: Pre-dipping prepares the surface of the print for etching, swelling surfaces to make them easier for the etching chemical to reach.
- Etching: After the part is ready, it's dipped into an etching solution, which etches the surface of the part, increasing the surface area by producing minuscule holes in the part's surface. This increased surface area promotes bonding between the plastic and deposited metal. Typically, the etchants involved in this process consist of chromic acid-based etchants — almost 90 percent of all plastic plating methods use acrylonitrile-butadiene-styrene (ABS).
- Neutralizing: After the surface of the part is properly etched, the part needs to be rinsed to remove any excess chemicals. This process is usually enhanced with the use of a neutralizing base like sodium bisulfite, which inactivates any remaining etchant on the surface of the part.
- Pre-activating: Once dry, the product is dipped into a pre-activator, which helps prepare the surface of the product for the activation step by facilitating absorption. This step tends to work best with prints made of polypropylene and polyphenylene oxide.
- Activating: Next, the part is introduced to a low-concentration precious metal liquid activator. This activator acts as the catalyst in the plating process, and usually contains precious metals like palladium, platinum or gold.
- Accelerating: Once activated, excess catalytic material needs to be removed from the part using an accelerator. This step helps prevent the occurrence of skip plating and tends to help improve the consistency of the finish.
- Bath Immersion: The final step is to apply the metal coating, which is accomplished by placing the print into the electroless bath containing the metal for coating. The catalyst added to the surface of the part in the activation step reacts with the solution in the bath, causing the molecules of metal to bond to the plastic molecules on the surface of the part. Typically, the metal involved is either nickel, copper or an alloy of either, though gold and silver can also be deposited using this method.
Are There Other Plating Options?
As previously stated, the plating process usually begins with an electroless plating process before another layer can be plated on. However, the pattern with which the part is plated can be altered according to the client's needs.
Electroless plating can be applied to a whole part or selective portions of a part. In the former option, the electroless plating process described above is applied to the entire surface of the part. This is usually the most cost-effective option, resulting in a metallic surface between 1 and 50 micrometers thick. Selective plating, however, involves depositing metal onto specific areas of a part, requiring alterations to the process above.
Instead of applying chemicals to the entire part, as with whole-part plating, selective plating requires applying these chemicals to parts of the substrate, leaving the other surfaces intact. Sometimes, these surfaces are even protected from these chemicals with a removable coating. As a result, when the electroless bath immersion step happens, the metal won't deposit on the untreated surfaces, leading to a partial coating between 1 and 10 micrometers thick. This process is typically more expensive than whole-part plating but has its own benefits for certain 3D part constructions.
What Materials Are Used to 3D Plate?
As previously discussed, plating onto 3D prints made of plastic requires an electroless process for the first layer. This usually involves nickel or copper, though it is possible to plate gold and silver with this method. Once this first layer is down, however, it's possible to plate just about any other metal on top of the first layer. That includes tin, platinum, palladium, rhodium and even chrome. You can even use electroplating on your 3D prints.
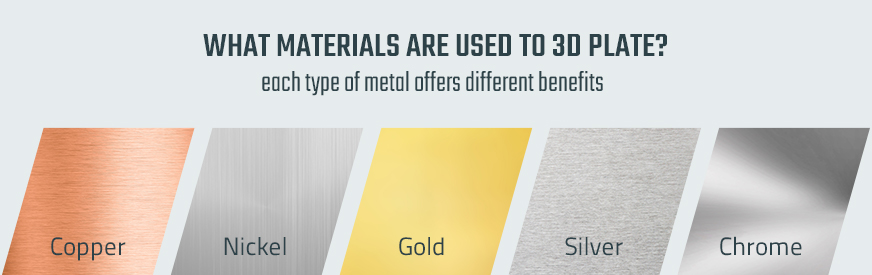
As far as which type of metal is best for finishing a 3D printed part, that depends on the purpose of the print. If the goal is aesthetic appearance, the plating will depend on the desired final look. If functionality is the goal, however, each type of metal offers different benefits:
- Copper: This conductive metal is a common choice, both for its appearance and for its industrial utility. Copper offers good heat transfer properties and can carry an electric current. It is, however, more vulnerable to the elements than other metals.
- Nickel: Exceptionally resistant to corrosion, nickel is an excellent choice in economical plating. Though less aesthetically appealing than gold or silver, nickel is affordable yet effective. It's worth noting that nickel is more likely to form pores, which can cause issues with corrosion if left unchecked.
- Gold: Gold is another common choice, both for its lovely finish and its functionality. Resistant to corrosion and oxidation, gold provides a good protective layer for plastics when applied in a thin layer. The material is also conductive. The main downfall of gold is its price.
- Silver: Another noble metal, silver is exceptionally beautiful and electrically conductive but expensive. It also tarnishes in the presence of oxygen, making it a less desirable exterior coating.
- Chrome: Particularly favored in the automotive industry for its aesthetically-pleasing finish, chrome plating is both decorative and functional as a final finish for 3D prints. Chrome provides a hard surface for the part, which is both easy to clean and highly resistant to corrosion. *Please note that Sharretts Plating does not plate with chrome. This content is for educational purposes only.
What Problems Occur in the 3D Plating Process?
The process of plating for 3D printed components is more involved than most. Naturally, several problems can occur during the plating process, each of which produces different results. Here are the most common of these issues:
- Poor Adhesion: Usually the result of insufficient etching, insufficient adhesion can lead to peeling of the metallic layer from the plastic. This usually occurs because the etchant's chemical makeup contains too much chromium.
- Warped Parts After Etching: Parts will sometimes warp during the etching process, which is usually a result of too much heat or too much tension on the rack during the etching step.
- Roughness After Activation: If a part has visibly rough edges after the activation step, it's a sign that foreign particulates or chemicals from the etching step got into the activation bath.
- Failure to Plate: Sometimes, large portions of a part won't plate, such as the edges or an entire side of the part. This is usually a result of over-acceleration if the edges won't plate, or under-acceleration if larger areas refuse to plate. Over-acceleration can be fixed by lowering the acceleration temperature while under-acceleration can be fixed by increasing it. If this fails, check the chemistry of the accelerator solution.
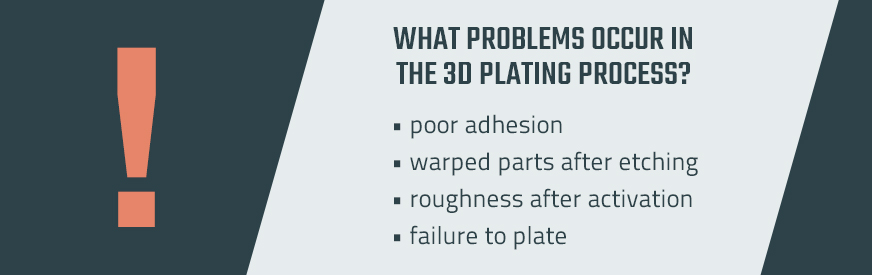
Choose Sharretts Plating for 3D Plating
At SPC, we have over nine decades of experience in a variety of plating applications, including industrial plating for 3D printed parts. We can perform surface finishing on 3D prints of all types and have done so for a variety of companies from a wide range of industries, including the automotive and consumer electronics industries. No matter what your company needs, we can develop a customized process for you.
Learn more about our company and our 3D plating processes by contacting us today, and discover what we can do for your company by getting a free, no-obligation quote for your project.
Additional Resources:
LEARN WHAT OUR MANY SATISFIED CUSTOMERS HAVE TO SAY ABOUT Us
"I would like to thank you for the help you have provided us in developing an electroless nickel plating technique on an unusual substrate. The sample platings you provided show that we should be able to reach our goals. I especially appreciate your willingness to take on an unusual job, with the uncertainties that that entails...We are looking forward to working with you in the future on our plating needs."
– Robert K.