Metal Plating for Defense Applications
The brave men and women who serve in our armed forces routinely are required to place themselves in harm's way, often in remote corners of the world. The quality of the equipment and machinery they use on a daily basis can make the difference between life and death. To protect our military personnel, the defense industry is always looking to ensure they have the best products available.
When manufacturing products for the military/defense industry, there is no margin for error. Machines such as tanks and armored personnel carriers must be built to exacting specifications, with no deviation permitted, to ensure they will be able to meet the rigorous demands of combat and other challenging conditions. High quality and exceptional durability of the finished products are also of utmost importance.
The Significance of Metal Finishing in Defense Industry Manufacturing
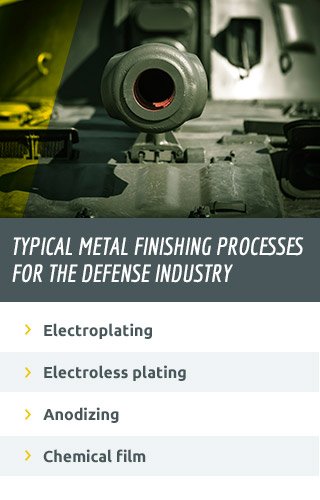
Proper finishing is an important component of any manufacturing process for metal products and machinery used in the defense industry. Finishing generally involves the application of a metal coating that adheres to the surface of the product and forms a protective bond. Typical metal finishing processes include:
- Electroplating: Electroplating uses a process called electrodeposition to form a protective coating on the surface of a metal part, which is referred to as the substrate. An electric current is introduced into an electrolyte plating solution (bath) containing dissolved ions of a metal or metal alloy. This causes the ions to be deposited onto the surface of the substrate.
- Electroless plating: As with electroplating, electroless plating applies an adherent coating to the substrate. The major difference is that no electric current is used in the process. Instead, coating occurs as the result of an autocatalytic chemical reaction that takes place in the plating bath. The electroless plating process enables greater control over the thickness of the metal coating and also produces a more even, uniform coating application.
- Anodizing: Anodizing is often used for protecting aluminum parts that are frequently used in the manufacturing of military/defense machinery and equipment. As with electroplating, the substrate is immersed in an electrolyte bath, which is followed by the passing of an electric current. The aluminum substrate serves as the anode (positively charged electrode), causing the release of oxygen ions from the bath. The oxygen ions combine with aluminum atoms and are fully integrated into the substrate's surface.
- Chemical film: Chemical film, also known as chromate conversion, involves the application of a chromate-based compound to the surface of the substrate. The process produces a film that adheres to the surface and serves purposes such as protecting against corrosion and promoting electrical conductivity. Chem film coatings are available in a wide range of colors including clear, blue, gold, iridescent, green and black.
Defense Plating Processes: What Types of Parts Can Be Protected?
Defense plating and other metal finishing processes can be used to protect many different parts including:
- Screws
- Fasteners
- Contacts
- Gun Barrels
- Detonators
- Avionics
- Missile components
- Aircraft engine parts
- Optical devices
- Shields
- Radar arrays
- Guidance system components
- Communication system components
What Are the Benefits of Defense Metal Finishing and Plating?
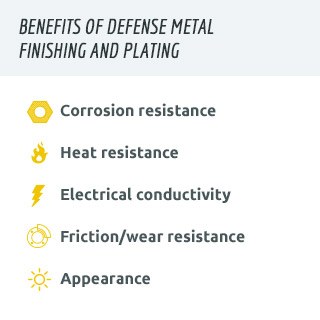
Defense plating techniques and metal finishing processes offer many essential benefits:
- Corrosion resistance: Many military vehicles, weapons and machinery are used in humid climates, which can accelerate rust. Metal coatings can serve as a sacrificial barrier that will prevent substrate corrosion from occurring, prolonging the lifespan of the parts.
- Heat resistance: Some defense industry equipment is susceptible to the buildup of heat during operation. A metal coating can make the part more resistant to extreme temperatures and prevent heat damage over time.
- Electrical conductivity: It may be necessary in some cases to enable the surface of a substrate to conduct electricity. The right coating can make a metal or plastic substrate electrically conductive in a cost-effective manner.
- Friction/wear resistance: Many types of military equipment are comprised of moving parts that come in contact with one another. The resulting friction and wear can lead to the premature demise of the equipment. A metal coating can lower the frictional coefficients between pieces, significantly reducing the impact of wear.
- Appearance: In some instances, the appearance of a product used for defense purposes is important. A metal coating can alter/enhance the appearance, while also providing some or all of the protective properties mentioned above.
Compliance With Military Specifications
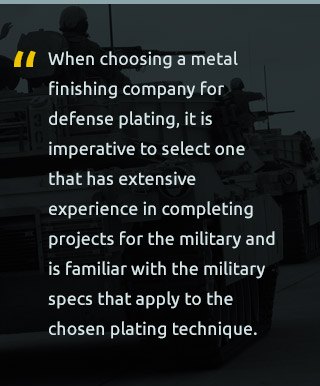
Metal plating for defense applications requires close adherence to stringent specifications developed by the Department of Defense. Metal finishing companies that receive defense contracts must meet these standards or risk having their work rejected.
an example, MIL-P-45209B pertains to plating with palladium. It details the standards and requirements for:
- Materials
- Pretreatment techniques
- Acceptable plating methods and equipment
- Various plating properties such as thickness, adhesion, smoothness
When choosing a metal finishing company for defense plating, it is imperative to select one that has extensive experience in completing projects for the military and is familiar with the military specs that apply to the chosen plating technique. The specifications can vary widely from one metal finishing method to another and are subject to frequent updating by the Department of Defense.
Military Plating Specifications: A Closer Look
MIL-DTL-45204D
MIL-DTL-45204D has replaced the MIL-G-45204C spec regarding gold mil-spec metal finishing. Specifically, the updated standard covers the requirements when electroplating gold onto other metallic surfaces. Examples of these requirements include:
- Materials and processes: The spec stipulates that the gold-plating product may produce a coating with either a matte or bright finish unless the contract indicates otherwise.
- Condition of the base metal: The substrate that receives the electrodeposited gold coating must be free of defects, pits, scratches and other surface imperfections that could prevent sufficient coating application.
- Surface preparation: The mil-spec plating service provider should ensure that gold plating only occurs after the execution of the applicable surface treatment/preparation processes, such as brazing, welding, machining and forming.
- Hardness and thickness: The acceptable Knoop hardness of the coating should meet the standard based on the grade of the underlying material (A, B, C or D), while the acceptable thickness is determined by the applicable class (00, 0, 1, 2, 3, 4, 5 or 6).
In addition, gold plating thickness standards apply under this military spec. The following eight classes correspond to the acceptable minimum thickness in inches:
- Class 00: 0.00002
- Class 0: 0.00003
- Class 1: 0.00005
- Class 2: 0.00010
- Class 3: 0.00020
- Class 4: 0.00030
- Class 5: 0.00050
- Class 6: 0.00150
MIL-C-26074E
MIL-C-26074E plating supersedes the previous I MIL-C-26074D specification regarding electroless nickel coatings. Highlights include:
- Materials: Electroless nickel coatings may be applied directly to aluminum, nickel, copper, cobalt, beryllium, iron, titanium and their alloys, as well as composite materials when using appropriate pretreatments.
- Hardness: When applying an electroless nickel coating to a steel substrate, the part or component should be measured for hardness based on ASTM E18 standards.
- Thickness: The acceptable coating thickness depends on the material being plated: grade A (0.0010 inches) for aluminum-based alloys; grade B (0.0005 inches) for nickel, cobalt, titanium, nickel and beryllium alloys; and grade C (0.0015 inches) for iron-based alloys.
- Corrosion resistance: All grade A electroless nickel coatings on aluminum alloys and grade C coatings on iron-based alloys must show no visible evidence of corrosion after testing.
This military spec has three minimum grade thicknesses, in inches, for the nickel coatings:
- Grad A: 0.0010
- Grade B: 0.0005
- Grade C: 0.0015
Exploring the Various Defense Metal Finishing and Plating Processes
Specific metal finishing processes include:
- Hard coat anodizing: Also known as Type III anodizing, hard coat anodizing is done in accordance with the MIL-A-8625 specification. The process uses sulfuric acid, low plating bath temperatures and consistent electric current rectification to produce an extremely hard protective coating that offers excellent corrosion, wear and abrasion resistance.
Depending on the composition of the underlying aluminum substrate, the coated part can range in color from light to dark gray. It is also possible to dye the finished part black if desired. Typical military hard coat applications include the manufacturing of ordnance and firearms. - Cadmium plating: Cadmium is a soft, silvery-white metal known for its excellent versatility. When plated onto cast iron, steel, copper, malleable iron or powdered metal parts, it provides superior corrosion protection by serving as a sacrificial coating. Cadmium plating can also create an exceptional bonding surface for adhesives, often making it the coating of choice for saltwater applications and the manufacturing of military aircraft.
However, the increasing awareness of protecting the environment is resulting in the gradual phasing out of cadmium in plating processes, due to its highly toxic nature. QQ-P-416C is the applicable military specification for cadmium plating. - Zinc-nickel plating: Zinc can be alloyed with nickel to create a protective coating on parts used to manufacture military vehicles in certain situations.
The zinc-nickel alloy is particularly effective when used on copper,Zinc-nickel is known as an efficient, cost-effective electroplating procedure that provides excellent corrosion protection. It can also provide excellent heat resistance, which is extremely useful in the manufacturing of engine parts and components for military vehicles. Zinc-nickel is often used as a substitute for cadmium plating in galvanic interaction applications. - Gold plating: Gold is a precious metal best-known for its glittery appearance and high economic value. Gold also offers important benefits in terms of industrial manufacturing.
Specifically, gold offers good corrosion and tarnish resistance, conducts electricity well and provides low contact resistance, which makes it suitable for many military-related electronics manufacturing applications. Gold is also an extremely solderable metal. The applicable military standard for gold electroplating is MIL-G-45204B. - Silver plating: Silver electroplating can provide an effective means of coating metals such as copper, bronze, aluminum, steel and stainless-steel alloys. Silver offers excellent solderability and is regarded as the best conductor of electricity.
Perhaps silver's biggest weakness is its susceptibility to tarnishing. Supplementary coatings may be used to reduce the impact of tarnishing. Although silver's ability to resist corrosion is regarded as good, the application of a nickel undercoating is recommended in situations where maximum corrosion resistance is required. The silver plating process can be tailored to produce a matte, semi-bright or bright finish to meet varied appearance preferences for military equipment and machinery. The military spec when plating with silver is QQ-S-365A. - Palladium plating: Like gold and silver, palladium is classified as a precious metal. Palladium is often referred to as "white gold" because of its shimmering, silvery-white appearance. Palladium is sometimes selected over gold for use in many defense metal plating applications due to its lower cost.
Palladium is typically used as part of a multi-layer plating process. The palladium serves as an anti-diffusion layer when copper is electroplated over gold. Palladium is also known for its good solderability. Because of its high melting point, palladium plating may be chosen for various types of connector applications used in defense manufacturing processes. The military specification when plating with palladium is MIL-P-45209B. - Copper plating: Using copper plating for defense applications can serve as a cost-effective metal-finishing alternative. It is primarily used in engineering applications to serve as a heat stop-off or mask. Key engineering properties provided by copper include superior electrical conductivity (as in copper electrical wiring), as well as good lubricity and solderability.
Copper is often used as undercoating when plating with precious metals such as gold, silver and palladium, as it adheres well to both the substrate and the metal coating. When used as an undercoat, copper provides good corrosion resistance. Electroplated copper finishes can range from matte to bright. The copper military specification is MIL-C-14550A. - Nickel plating: Nickel is a silvery-white metal offering the flexibility to provide finishes ranging from dull to extremely bright. It can also be used to create a soft or hard finish. Using nickel in military plating applications can enhance the corrosion and wear resistance of the substrate. The applicable military spec for nickel electroplating is QQ-N-290A.
A commonly used nickel plating variant for engineering applications is sulfamate nickel plating. Sulfamate plating can facilitate the process of forming a seal between two metallic surfaces. Because it produces a dull finish, sulfamate nickel plating is not recommended for substrates that need aesthetic appeal. The applicable military specification for sulfamate nickel plating is MIL-P-27418. - Electroless nickel plating (ENP): ENP is a good choice for many high-precision military metal finishing applications. The electroless plating process provides a uniform finish that can infiltrate areas on the surface that are out of reach when using traditional electroplating processes.
ENP is often applied to aluminum parts and components used to manufacture various types of military equipment to enhance wear and corrosion resistance, as well as for oddly shaped parts that cannot be electroplated effectively. Low-, medium- and high-phosphorous electroless nickel formulas are available - the higher the phosphorous content, the greater the corrosion resistance. The military specification for electroless nickel plating is MIL-C-26074B. - Chemical film: Chem film coatings are primarily used for corrosion protection on aluminum parts for defense equipment that requires no dimensional change to the substrate. In addition, a Class 1A chem film will improve paint adhesion when applied as an undercoating before painting. A Class 3 chem film is used in electronics and electrical applications that require low contact resistance.
The MIL-C-5541B specification applies to the actual coating, while any materials used during the process must conform to MIL-C-81706 requirements. Additionally, the coated surface must be free of imperfections such as chips, breaks or scratches.
Request a free quote
For Defense Plating
The Importance of Choosing an Experienced Metal Finishing Company
Because of the high level of precision and expertise required in all defense plating and metal finishing processes, it is crucial to select a company that has extensive experience in the various defense plating procedures. Sharretts Plating Company (SPC) has been in business since 1925. We have the ability to create a customized metal finishing process ideally suited for your operation.
SPC has been an ISO-certified company since 1994, which demonstrates our sincere commitment to developing and implementing high-quality metal finishing processes. We also have the proud distinction of receiving the Department of the Navy's Best Manufacturing Practices Award. Our team developed all of our processes in compliance with current defense/military specifications.
We're at the Forefront of Defense Plating Innovation
As part of our ongoing effort to respond to the needs of our numerous defense industry clients, SPC is always striving to upgrade our metal finishing processes. One of our most recent innovations is the development of a revolutionary black electroless plating process known as SMITH-EN-BLACK™.
Recognizing that the Department of Defense had started to require the inclusion of black coatings on many products to promote light and energy absorptions, we created a low-phosphorous black electroless nickel product that is far superior to black oxide or chromates. We have the capacity to apply SMITH-EN-BLACK™ to high-volume defense industry manufacturing processes.
Additional Resources:
Get a Free Quote from SPC for Metal Plating in Defense Applications
Get a free quote today for our wide range of defense metal plating solutions that can benefit your unique defense industry manufacturing operation. We'll be happy to schedule an on-site defense plating consultation at your facility.
LEARN WHAT OUR MANY SATISFIED CUSTOMERS HAVE TO SAY ABOUT Us
"I would like to thank you for the help you have provided us in developing an electroless nickel plating technique on an unusual substrate. The sample platings you provided show that we should be able to reach our goals. I especially appreciate your willingness to take on an unusual job, with the uncertainties that that entails...We are looking forward to working with you in the future on our plating needs."
– Robert K.